5 Types of Electrical Lug and Applications: Precision Components Connecting the World of Electricity
In modern electrical systems, every detail is critical. From large-scale power stations to household electricity, the stable transmission and distribution of power relies on a series of sophisticated electrical components. A key role is played by electrical lug, also known as cable terminals or cable connectors, which are the basis for ensuring the safe and efficient transmission of electricity. In this article, we will explore the different types of electrical lugs, their applications, and their features.
Classification of Various Lugs/Terminals
Copper Terminal
Copper lugs are ideal for large gauge applications for power consumption or grounding. Wires can be soldered or crimped to each copper terminal. One end of the copper terminal connects to the cable by soldering, welding, or crimping, depending on the type of lug used. The other end of the copper lug is secured to a matching termination or connection point by bolts, screws, or spring clips.
Copper electrical lugs are easy to install and offer long-term reliability. WZJ copper lugs are made of high-grade ETP copper and are tinned to prevent corrosion. Perfect for any outdoor application or marine environment.
Available in cable sizes ranging from 1.5 mm² to 1000 mm², our electrical lugs offer a reliable and fast termination method for interconnecting large format power cables to busbars, relays, batteries, solar inverters, power cables, grounding devices and more, increasing efficiency, safety, and reducing costs.
Aluminum Lug
Aluminum terminals are made from solid aluminum rods using high conductivity (99.6% pure) aluminum. Lugs are forged from solid material and are suitable for outdoor use (as the palm end is sealed). Aluminum terminals come with joint compounds in the barrel and are sealed with end caps. A list of standard sizes is available but can be fabricated upon request. Crimping is done using a hexagonal die and the usual aluminum cable preparation.
However, copper terminals are better in many ways. These terminals are a little more expensive than aluminum lugs. Aluminum cables and lugs are found in almost every wiring system due to their low price. Innovations related to aluminum lugs are underway to make them as safe and convenient as copper lugs.
Aluminum terminals are plated with an intermediate layer of copper coating to prevent corrosion and are chamfered at the end of the barrel entrance for easy insertion into the barrel.
The inner barrel of the lug contains an antioxidant compound that reduces the formation of oxides internally, helping to achieve a better connection when the terminal is crimped to the conductor; however, UL-approved aluminum terminals carry the AL9CU mark and are rated for 90 C systems.
Bimetallic Lug
Bimetallic lugs are friction-welded, where the aluminum barrel is friction-welded to the copper barrel for an optimal transition between barrel and barrel, creating a high-quality connection between the copper barrel and the aluminum barrel. Bimetallic lugs are used in solar power plants to connect aluminum conductors to copper busbars in a range of electrical applications such as control panels, switchgear, and converter boxes.
As a result, the aluminum conductor contacts the aluminum barrel, and the copper busbar contacts the copper palm. To prevent oxidation, the lug barrel is filled with a contact lubricant that improves contact properties for a smooth electrical connection.
We manufacture a wide range of lugs, connectors, and specialized products to meet specific customer needs. Other combinations are available if required:
- 1-Bimetallic lugs – Aluminum barrels with copper pallets (single, double, or four holes)
- 2-Bimetallic lugs with copper washers (aluminum lugs with copper washers)
- 3-Bimetal lugs reverse type (copper barrel with aluminum palm)
- 4-Bimetallic connectors – straight type (for aluminum and copper cables of the same cross-section)
- 5-Bimetallic connector – reducer type (for aluminum and copper cables with different cross sections)
- 6-Bimetallic connectors – pin type (aluminum barrel with solid copper pin)
Crimping lugs
Crimping is the process of deforming one or both of two pieces of metal or similar material to hold the other in place. This bending or deformation is called crimping.
Crimp terminals are connectors that join cables, surfaces, and machinery. Clamps that connect wires to automotive batteries and the ends of battery jumper cables are examples of crimp lugs.
They are used in automotive wire systems, electrical boxes, machinery, home appliances, electronics, and other durable goods. For electrical applications, insulate them with rubber or plastic. They prevent accidental energy transfer to people or neighboring electrical components.
Mechanical lugs
Mechanical connector technology is the best way to connect cable conductors, using cutting-edge technology such as shear bolt connectors. Here, the bolt head is sheared off at a predetermined torque. These mechanical connectors or shear bolt connectors are made of certain alloys.
These connectors have a sleeve and lug body which are made of high-strength aluminum alloy. The inner surface of the connector has grooves and the sleeve is suitable for underground use. The terminals are available in a variety of hand-hole sizes and fit both externally and internally. These products are also available in low, medium, and high-voltage versions.
Compression Lugs VS Mechanical Lugs
Compression lugs are suitable for small electrical work and large mechanical work (buildings or large commercial cables). Compression lugs are much smaller than mechanical lugs. Mechanical lugs connect large wires, such as cable wires. Due to their construction and design, they are used in automobiles. When wire connectors are needed, compression terminals are commonly found in residential and small business structures.
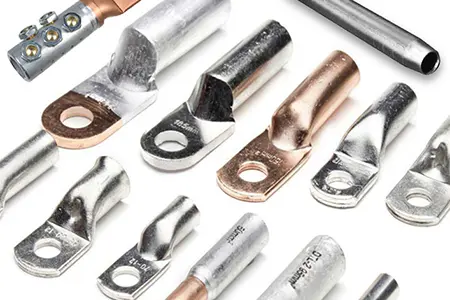
Features and characteristics of various types of cable terminals
a) Entry into the cable drum has a mechanical pull test and an electrical durability test. The vibration-proof portion of the entry is flared for smooth wire insertion.
b) Cable ends are tested for high current at 250°C temperature. High-quality materials provide optimum electrical conductivity, high load capacity, and enhanced safety.
c) Flat contact surfaces and internal chamfers allow for simple, secure connections. Copper lugs are annealed to specific temperatures for improved material properties and better crimping.
d) All copper parts are tin-plated to BS specifications to protect against corrosion and oxidation, and terminals are insulated with PVC for excellent dielectric strength and support.
e) Copper tubing sizes are customized to fit specific square millimeters of cable to ensure complete electrical conductivity and mechanical strength to withstand vibration and tension.
Range of sizes of electrical lugs
Cable lugs, also known as cable terminals, are components of electrical equipment used to connect cables to device terminals. It simplifies the assembly, maintenance, and repair process for personnel. Cable ends or connectors are used when a permanent connection is required, but a direct connection is not convenient or possible. In this blog, we will learn about the types of lugs, their applications, and their functions.
Lugs are made of high-grade electrolytic copper (ETP grade) and are available in a variety of diameters and mounting holes, with wire sizes ranging from #8AWG to 1000MCM. The terminals are CSA and UL-certified and have corrosion-resistant tin plating.
Applications of different types of lugs
Cable lugs make installation, repair, and maintenance of electrical equipment and cables easy. They connect two wires or connect more than two cables. They also connect fuse sockets, load switches, and electrical equipment. Insulated lugs with a pin, tab, hook, fork, and ring terminals are used in the wire, automation, control panel, and instrumentation industries. Copper ring lugs are used for a variety of connection reasons. Copper cable ends connect multiple gadgets via cables.
Butt connectors and parallel connectors are other forms of lugs that connect and terminate two cables. PVC insulated, butt, heat-shrink, and enclosed are the most commonly used butt and parallel connections. It comes in a variety of sizes, shapes and materials. Depending on the type of cable used to connect one item to another, copper cable terminals are used as butt connectors and parallel connectors.
Lugs have an indispensable use in the wire and electrical field. They need to be tested for strength before they are applied to heavy machinery. The strength and design of connectors are critical in many applications. Ensure that you choose the right lugs for the intended use.
They are commonly used to connect distribution boxes and transformers to cables. Terminations in LV/MV connections terminate all cables and electrical switches in vibrating environments. It is used in transformers, motors, generators, batteries, switchboards, and other industrial applications. Especially in control panel cabinets to terminate flexible control wires to meters, connectors, and terminal blocks.
Applications in a wide range of industries and systems
- Power Distribution Systems: Electrical lugs are used in power distribution systems to connect cables to bus bars, transformers, circuit breakers, and other electrical components. They ensure reliable and efficient power transmission.
- Renewable Energy Systems: In solar power plants and wind farms, electrical lugs are used to connect solar panels or wind turbines to the electrical grid. They play a crucial role in transmitting the generated power to the distribution network.
- Industrial Machinery: Electrical lugs are essential in industrial machinery for connecting motors, generators, control panels, and other electrical equipment. They provide secure and stable connections, ensuring the smooth operation of the machinery.
- Automotive Wiring: In the automotive industry, electrical lugs are used in wiring harnesses to connect various electrical components, such as batteries, alternators, starters, and lights. They ensure reliable electrical connections in vehicles.
- Construction and Infrastructure: Electrical lugs are widely used in construction and infrastructure projects for electrical wiring and grounding. They are used to connect cables to electrical panels, junction boxes, and grounding systems, ensuring safety and efficient electrical distribution.
- Marine and Offshore Applications: Electrical lugs are utilized in marine and offshore environments, where they need to withstand harsh conditions, including saltwater corrosion. They are used in shipbuilding, offshore oil rigs, and other marine applications.
- Data Centers: In data centers, electrical lugs are used to connect power cables to server racks, power distribution units (PDUs), and backup generators. They ensure reliable power supply to critical IT infrastructure.
- Residential Electrical Systems: Electrical lugs are used in residential electrical systems for connecting cables to circuit breakers, electrical outlets, and light fixtures. They provide secure and efficient electrical connections within homes.

Frequently Asked Questions (FAQs)
Q1: What is the difference between copper lugs and aluminum lugs?
Copper lugs are made of high-grade electrolytic copper and offer excellent conductivity and corrosion resistance. They are ideal for large gauge applications and are commonly used in power draw or grounding. Aluminum lugs, on the other hand, are made of high-conductivity aluminum and are more cost-effective. They are suitable for outdoor use and are often used in wiring systems. Both types of lugs have their advantages and are chosen based on specific requirements.
Q2: Can different types of lugs be used together?
In some cases, different types of lugs can be used together, depending on the specific application and compatibility. However, it is important to ensure that the lugs are properly rated for the voltage and current requirements of the system. It is recommended to consult with a qualified electrical engineer or refer to the manufacturer’s guidelines for proper usage.
Q3: How are electrical lugs installed?
Electrical lugs can be installed using various methods, including soldering, welding, crimping, or bolting. The installation method depends on the type of lug and the specific application. It is important to follow the manufacturer’s instructions and industry standards for proper installation to ensure a secure and reliable connection.
Q4: Are electrical lugs reusable?
In general, electrical lugs are designed for one-time use. Once they are crimped or soldered onto a cable, they are not intended to be removed and reused. Reusing lugs can compromise the integrity of the connection and may lead to electrical hazards. It is recommended to use new lugs for each installation to ensure optimal performance and safety.
Q5: How do I choose the right size of electrical lugs for my application?
Choosing the right size of electrical lugs is crucial for ensuring a proper and secure connection. The size of the lug depends on the wire size and the c
Need electrical lugs? We’re here for you!
If you’re looking for high-quality, reliable electrical lugs or need a professional, customized solution, we’re ready to assist. Our team has the experience and technical knowledge to provide a lug product that meets your specific needs. Whether it’s a standard size or a special customization, we can ensure that you get the most suitable electrical connection solution. Contact us today and let us help you ensure the stability and safety of your electrical system.
Website: https://www.wzjelec.com/
Product: https://wzjelec.com/product
Email: rose@sunjelec.com