Polymer Insulators – Design, Applications and Mechanisms
Initially, polymer insulators were made of materials such as ceramics and glass. However, in 1963, a new type of polymer was introduced. However, recent improvements in design and manufacturing have made them popular with power companies and utilities. These insulators have a fiberglass core and are covered with a protective part made of a rubber material such as silicone, PTFE or EPDM. They also have metal parts for attachment at both ends. In addition, they are known as composite insulators, which combine at least two different insulating materials, a robust core and a protective shell with end fittings.
In this blog, we will take a closer look at these insulators, especially 11 and 33 kV.
Why are “polymers” considered insulators?
Polymers are considered “insulators” due to their molecular structure, which does not allow the free flow of electrons. This resistance to the movement of electrons means that electrical charges cannot easily pass through these materials.
In terms of thermal insulation, the valence electrons in these polymers are tightly bound to their atoms, preventing them from conducting heat. In addition, polymers can have high dielectric strength, which refers to the ability of a material to withstand an electric field without breakdown. This property makes them excellent at resisting the flow of electric current.
Additionally, electrical polymer insulators are materials that are the opposite of conductors – they block electrical currents. These insulating materials are vital in the electrical and electronics industry to prevent electrocution and ensure circuits operate safely and efficiently.
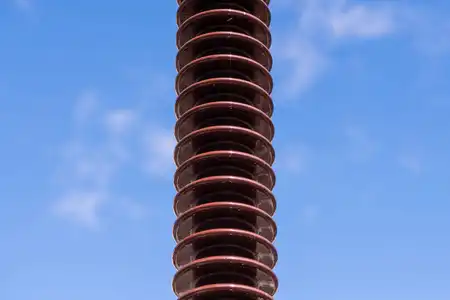
Applications for Polymer Insulators
These polymer insulators are chosen for their ability to resist electrical conductivity in high-voltage situations, such as in power lines, transformers, and other electrical equipment. These insulators are usually made of materials such as silicone rubber, polyethylene or epoxy resins. Their hydrophobicity and ability to prevent pollution-related flashovers make them critical in maintaining grid reliability.
Key properties that define polymer insulators include their low electron mobility and high current resistance, which help minimize the risk of thermal shock.
Let’s look at the materials used for these insulators:
- Plastics (resins)
- Organic Silicon
- Rubber
- Oil
- Glass (ceramic forms)
- Pure deionized water
These materials are chosen for their high resistance to electrical currents, making them ideal for insulation purposes, such as coatings for copper wire used in a variety of electrical applications, from household appliances to high-voltage power lines.
The effectiveness of an electrical conductor depends on the abundance of free electrons that move freely at room temperature, thus facilitating the flow of current. Polymer insulators, on the other hand, have few free electrons, significantly reducing electron movement and thus resisting current flow.
To illustrate this with a familiar material, let us consider wood. Wood can act as an insulator up to a certain voltage threshold. Beyond this threshold, wood may no longer act as an effective insulator and can begin to conduct electricity.
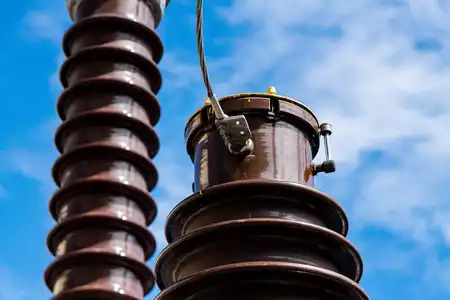
Components of a polymer insulators
1) Fiberglass Mandrel
The fiberglass mandrel sits at the heart of the polymer insulator design and serves two key functions. It provides primary mechanical strength and electrical insulation. The mandrel is made from thousands of fine glass fibers, called rovings, which are tightly bound together using epoxy resin. This combination ensures that the mandrel can withstand significant mechanical stress while effectively insulating against electrical currents. The integrity of the fiberglass mandrel is important because it directly affects the overall durability and performance of the insulator.
2) Rubber casing and windbreak
The core bar is surrounded by a rubberized casing that, in combination with a windbreak canopy, protects the core from environmental factors such as salt, dirt, dust and moisture. These components are essential to maintain the insulating properties of the insulator over time, preventing degradation that could lead to failure. Over the years, materials used for rubber housings have evolved, with silicone, EPDM (ethylene propylene diene monomer) and various alloys being the most common. Silicones are particularly valued for their hydrophobicity, which helps to waterproof and prevent moisture from accumulating on insulator surfaces, thereby reducing the risk of contamination flashovers.
The combination of these components in a polymer insulator produces an efficient insulating device that is lightweight, durable and capable of operating in a wide range of environmental conditions.
3) End Fittings
End fittings are the metal parts of the polymer insulator that connect it to the surrounding infrastructure. The material and design of these fittings are selected based on the insulator’s Specified Mechanical Load (SML) rating. For higher SML ratings, steel (cast or forged) is typically used because of its excellent strength, while ductile iron can be used for lower SML ratings. To protect against damage caused by environmental exposure, such as corrosion and rust, both iron and steel fittings are coated with protective galvanizing.
Originally, polymer insulators were produced using a method in which the end fittings were bonded to the mandrel with epoxy resin. These early designs were known as the “wedge style” and featured end fittings shaped like cups to hold the epoxy as it cured.
While some of these older models are still in operation, advances in technology have shifted the preference to compression technology, which causes the end fittings to curl. This modern technology allows for a more efficient and reliable process that produces smaller, lighter-end fittings without compromising strength ratings.
Note that end fittings vary greatly from one polymer insulator to another, and the type of connection they make is one of the few standardized aspects. These standards typically define several common connection types, including:
- Sleeve and Ball: This is the most tightly defined set, with both ANSI and IEC standards providing comprehensive specifications.
- Y-type U-clamp/ball: commonly used in the U.S.
- Oval eye/oval eye
- U-Clip/Tongue: another well-defined set, commonly used in international settings.
- U-Clip/Clevis.
Although the design of these connection ends is largely standardized, at Axis Electric certain aspects (such as the specific dimensions of the end fitting cartridges) can be customized to your requirements. The standards for these connection types, particularly sockets and balls, are very detailed and include “pass and fail gauges” for precise measurements. Other types, such as U-clamps/tongues and U-clamps/clamps, are also well-defined but can be tailored for your international use or to meet your unique specifications, including non-standard SML ratings.
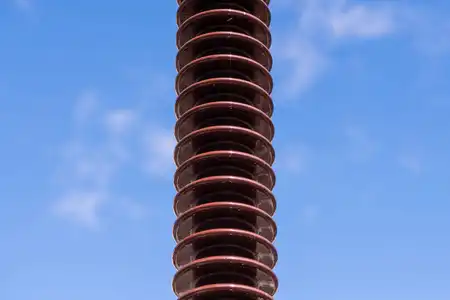
Design and Evaluation of Polymer Insulators
Key dimensions that must be considered when designing and evaluating polymer insulators, regardless of the assembly method, include:
- Dry Arc Distance: the straight line distance along the insulating surface between the metal fittings at each end of the insulator. This measurement is critical in determining the insulator’s ability to withstand arcing under dry conditions.
- Leakage (creepage distance): the total length of the path along the insulating surface between the metal fittings, which is longer than the dry arc distance due to the undulating shape of the windbreak. A greater leakage distance improves insulator performance in wet conditions and polluted environments by providing a longer path for potential leakage currents.
- Rubber (Insulation) Length: The length of the rubber casing covering the fiberglass core, directly affects the insulator’s overall insulation capability.
- Section/connection length: The length of the sectioning material or the connection between the windbreaks affects the insulator’s efficiency in preventing the accumulation of dust and moisture, and therefore its electrical insulation performance.
- These dimensions are essential to optimize the electrical performance of polymer insulators, ensuring that they meet the required standards for high-voltage electrical applications.
FAQ
1. What are the advantages of using polymer insulators over traditional ceramic or glass insulators?
Polymer insulators offer several advantages over traditional ceramic or glass insulators. These include:
- Lightweight: Polymer insulators are significantly lighter than their ceramic or glass counterparts, making them easier to handle and install.
- High mechanical strength: The fiberglass core of polymer insulators provides excellent mechanical strength, allowing them to withstand high mechanical loads and environmental stresses.
- Resistance to pollution flashovers: Polymer insulators have hydrophobic properties that prevent the accumulation of moisture and reduce the risk of pollution-related flashovers.
- Enhanced durability: The combination of materials used in polymer insulators, such as silicone rubber and epoxy resins, provides excellent resistance to UV radiation, chemicals, and environmental factors, ensuring long-term durability.
- Cost-effective: Polymer insulators often have a lower cost compared to traditional ceramic or glass insulators, making them a cost-effective choice for electrical infrastructure projects.
2. Can polymer insulators be retrofitted onto existing infrastructure?
Yes, polymer insulators can be retrofitted onto existing infrastructure. Their lightweight design and flexibility make them suitable for retrofitting onto existing structures without significant modifications. However, it is important to consult with experts and conduct a thorough assessment of the existing infrastructure to ensure compatibility and proper installation.
3. Are polymer insulators environmentally friendly?
Polymer insulators are considered environmentally friendly due to several reasons. Firstly, their lightweight design reduces the carbon footprint associated with transportation and installation. Secondly, the materials used in polymer insulators, such as silicone rubber and epoxy resins, are non-toxic and do not pose a threat to the environment. Lastly, the long lifespan and durability of polymer insulators contribute to reducing waste and the need for frequent replacements.
Conclusion
Choosing the right polymer insulator design can be tricky, as there are many different materials and options available. It’s best to consult with one of our engineers to help you choose the most effective design. You need to have a clear list of what you need, including what materials should be used and the exact dimensions of the part. It is vital to understand all the options for polymer insulator design and how they affect the insulator’s use.
Website: https://www.wzjelec.com/
Product: https://wzjelec.com/product
Email: rose@sunjelec.com