3 Reasons Why Insulation Piercing Connectors Reduce Transient Resistance – IPC Guide
In other words, they allow current to flow through the network without interruption.Insulation Piercing Connectors are popular because they are easy to install, they do not require special tools, they do not have to be stripped of cable insulation, and the network stays insulated from contact voltage after installation. Any heat generated on the distribution network is considered a loss. The most important thing is to achieve a safe and efficient connection with as little loss as possible. Transient resistance impedes the flow of current and transient resistance converts electrical energy into heat. Due to the large number of distribution connections, it is important to minimize losses as much as possible.
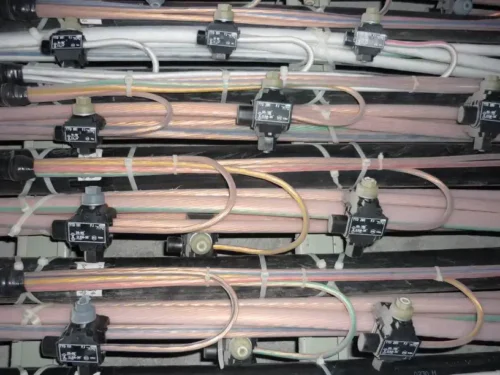
What are Insulation Piercing Connectors?
Insulation Piercing Connectors are specialized devices designed to establish a secure electrical connection by piercing through the insulation of cables. This innovative approach eliminates the need for stripping the insulation, simplifying the installation process while ensuring a robust connection.
Understanding Transient Resistance
What is Transient Resistance?
Transient resistance refers to the temporary increase in electrical resistance that occurs when there is a change or disturbance in an electrical circuit. This can lead to inefficient current flow, energy loss, and potential damage to electrical components.
Causes of Transient Resistance in Electrical Connections
Transient resistance can be caused by poor connections, corrosion, loose fittings, and environmental factors such as temperature fluctuations and vibrations. Addressing these issues is crucial for maintaining efficient and reliable electrical systems.
Why Insulation Piercing Connectors Reduce Transient Resistance
Reason 1: Direct Contact with Conductors
One of the primary reasons IPCs reduce transient resistance is their ability to pierce through cable insulation and make direct contact with the conductors. This direct contact ensures a secure and efficient electrical connection, minimizing resistance.
Benefits of Direct Conductor Contact
Improved Current Flow
By establishing direct contact with the conductors, IPCs facilitate better current flow. This reduces the likelihood of energy loss and ensures that electrical power is transmitted more efficiently across the connection.
Reduction in Energy Loss
The direct contact achieved by Insulation Piercing Connectors minimizes resistance at the connection point, reducing energy loss and improving the overall performance of the electrical system. This is particularly important in applications where energy efficiency is a priority.
Reason 2: Enhanced Connection Stability
Insulation Piercing Connectors are designed with mechanical strength in mind. Their robust construction ensures that once the connection is made, it remains stable and secure. This mechanical strength is essential for maintaining a low-resistance connection over time.
Resistance to Vibrations and Environmental Factors
Longevity of Connections
The stability provided by IPCs means that connections are less likely to degrade over time. This longevity ensures that the electrical system continues to perform efficiently, reducing the need for frequent maintenance and repairs.
Consistent Electrical Performance
IPCs are designed to withstand environmental factors such as vibrations, temperature changes, and moisture. This resistance to external influences helps maintain consistent electrical performance, further reducing transient resistance.
Reason 3: High-Quality Materials and Design
Insulation Piercing Connectors are typically made from high-quality materials such as copper and aluminum, which offer excellent conductivity and durability. These materials ensure that the connectors provide a low-resistance path for electrical current.
WZJ Design Features that Minimize Resistance
Corrosion-Resistant Coatings
Many IPCs are coated with materials that resist corrosion, ensuring that the connectors remain in good condition even in harsh environments. This corrosion resistance is crucial for maintaining a low-resistance connection over time.
Precision Engineering for Optimal Performance
The design and engineering of IPCs are focused on minimizing resistance and maximizing performance. Precision manufacturing techniques ensure that each connector fits perfectly, providing a secure and efficient electrical connection.
WZJ Insulation Piercing Connectors
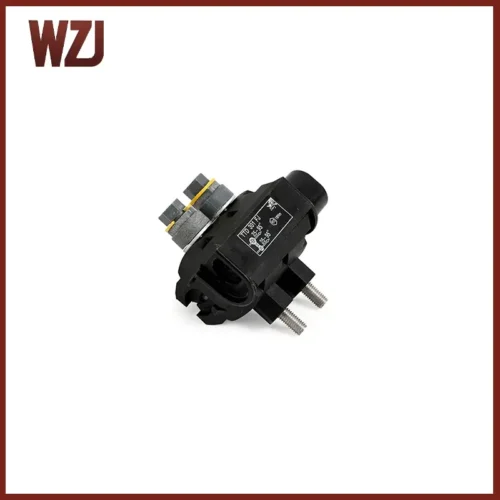
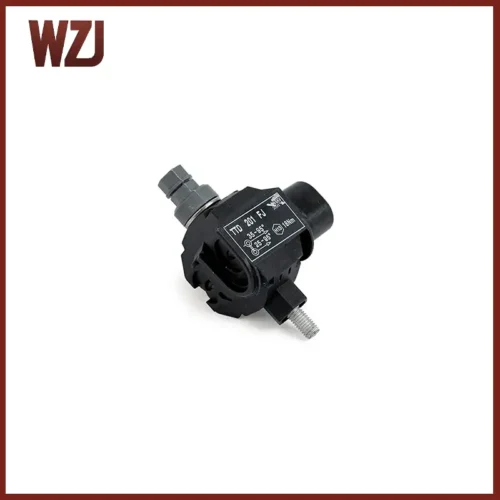
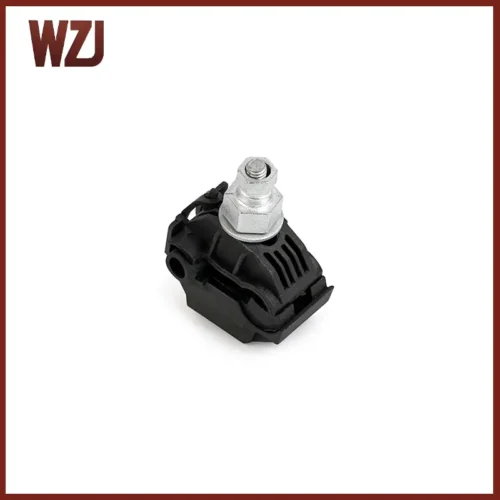
Geometry and Design of WZJ IPCs
How can we make WZJ IPCs more energy efficient and at the same time reduce network losses?
The design, geometry, and type of material of the contact plate are very important as it is the point of contact between the conductor and the connector. The type of material is important because the resistance of the connector itself depends on it, as well as the amount of energy required to transfer electrons from the conductor to the contact plate and back. The design and geometry of the contact plate are important because they affect the depth of the contact plate into the conductor. They also have a significant effect on the amount of energy required to move the electrons, especially as they pass from the conductor to the contact plate and back.
Waterproof Insulated Puncture Connectors
There must be no moisture at the contact point, no matter how much time has passed since installation. If moisture is present at the point of contact, it can lead to electrolytic corrosion where the copper and aluminum are joined, and if moisture is present at the point of contact, it can lead to aluminum oxidation where the two aluminum conductors are joined. Both of these chemical processes significantly increase the transient resistance at the contact point and lead to significant heat generation.
WZJ IPC connectors are designed in such a way that thanks to several technical details, they do not allow moisture to penetrate. In addition, they are protected by electrical contact grease. We always emphasize that after installing WZJ IPC connectors, an end cap must be placed at the end of the branching conductor to prevent moisture from passing through the conductor to the contact point.
Simple installation
To achieve the high-efficiency factor of the connector, the installation must be simple, regardless of the site and working conditions at height. WZJ IPC connectors have several implemented technical details that allow them to be easily mounted on the conductor, to achieve a good connection by simple fastening, and to require no additional fastening after installation, regardless of the weather conditions, i.e. the connection does not need to be calibrated. The WZJ Insulation Piercing Connector can be installed in temperatures from -22 to +45 degrees Celsius. It has been tested even at -50 degrees Celsius, although the insulation of the ABC itself hardens by 45%.
Routine testing
It is important to keep checking and reconsidering the results so that good connectors become better. We strive for zero electrical loss in our connectors and the WZJ IPC has been subjected to numerous tests derived from the EN 50483 and NFC 33020 standards, as well as numerous factory tests that we have developed. The video below shows a transient resistance of 5.4 μΩ, which is one of the best results in the world of competition. Due to the high efficiency of our IPCs, minimizing transient resistance results in fewer network losses, which is one of the main goals we are actively working towards.
WHY CHOOSE WZJ INSULATION PIERCING CONNECTORS
WZJ was established in 2004 and has been manufacturing Insulation Piercing Connectors since 2015 and has experience in many international projects.
Here are some of the factors that make WZJ one of the best manufacturers and why you should buy IPCs from WZJ.
- Product Quality and Reliability: WZJ produces high-quality Insulation Piercing Connectors that are reliable and durable.
- Compliance and Certification: WZJ Energy ensures that the Insulation Piercing Connectors comply with relevant industry standards such as NFC 33-020, and EN-50483, giving customers confidence in the quality and safety of their products.
- Product Range: WZJ Energy offers a wide range of Insulated Puncture Connectors for 1kv power lines to meet various application requirements.
- Research and Development: WZJ Energy invests in research and development to continually improve the design, performance, and reliability of its Insulated Puncture Connectors to ensure they remain competitive in the marketplace.
- Customer Support: WZJ Energy offers strong customer support including technical assistance, flexible OEM with sticker, and after-sales service, which is important to customers looking for reliable application solutions.
contact us
Conclusion
Insulation Piercing Connectors play a crucial role in reducing transient resistance in electrical systems. By making direct contact with conductors, providing enhanced connection stability, and being constructed from high-quality materials, IPCs ensure efficient and reliable electrical connections. Whether used in residential, commercial, or industrial applications, Insulation Piercing Connectors offer a range of benefits that make them an invaluable component in modern electrical installations.
FAQs About Insulation Piercing Connectors
What is the primary function of an Insulation Piercing Connector?
The primary function of an IPC is to establish a secure electrical connection by piercing through the insulation of cables without the need for stripping, ensuring efficient and reliable power transmission.
How do Insulation Piercing Connectors improve electrical connections?
IPCs improve electrical connections by making direct contact with the conductors, enhancing connection stability, and are made from high-quality, conductive materials that minimize transient resistance.
Are IPCs suitable for outdoor applications?
Yes, IPCs are designed to withstand various environmental conditions, including extreme temperatures and moisture, making them suitable for outdoor applications.
What types of cables can IPCs be used with?
IPCs are compatible with a wide range of cable types, including copper and aluminum cables, making them versatile for different electrical systems and applications.
How do I choose the right IPC for my needs?
When choosing an IPC, consider factors such as the type of cables, environmental conditions, and specific project requirements. Look for connectors that meet industry standards and are certified for your application.
Website: https://www.wzjelec.com/
Insulation Piercing Connectors: Piercing Connector – wzjelec.com
Email: rose@sunjelec.comAuther: Leb