7 Key Points for Good Earthing System: Ensuring Electrical Safety
A good earthing system plays a key role in protecting buildings, equipment, and people from the damaging effects of lightning strikes. Because of the rapid rise time and high currents that characterize lightning strikes, special care needs to be taken when designing and implementing an earthing system. This guide will walk you through the basic characteristics of earthing systems, the importance of soil resistivity, various grounding methods, and maintenance practices. We will also discuss relevant codes and standards and provide practical examples to demonstrate the effectiveness of proper grounding solutions.
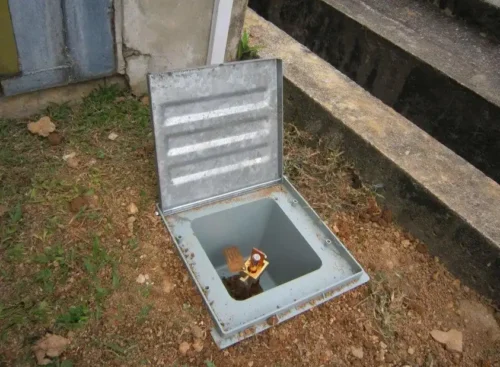
7 Key Characteristics of a Good Earthing System
Electrical conductivity
The system must have a low electrical resistance for lightning currents to dissipate efficiently into the ground. The use of conductive materials such as copper, aluminum, or galvanized steel in the design of the grounding electrode and conductor ensures low resistance and optimal performance
High fault current withstand
Earthing conductors should be able to withstand high fault currents. Choosing a material with high tensile strength and sufficient cross-sectional area will ensure that the conductor can withstand the stresses caused by lightning surges.
Long service life
The service life of the system should be at least 40 years. This can be achieved through the use of corrosion-resistant materials and proper installation techniques to minimize damage over time.
Low grounding resistance and impedance
Maximizing the surface area of the electrode and conductor in contact with the surrounding soil helps to reduce grounding resistance and impedance. This can be accomplished using techniques such as multiple interconnecting ground rods, radial conductors, or buried floors.
Equipotential Connections
Equipotential connections are essential to minimize dangerous potential differences between input conductors such as metallic water supply systems, electrical power systems, and telecommunication systems. This practice helps to reduce step and contact potentials and ensures the safety of personnel.
Corrosion resistance
Grounding electrode systems should be corrosion-resistant and compatible with other conductors buried in and connected to the earthing system. The use of materials such as copper or galvanized steel and proper installation techniques can help reduce the risk of corrosion.
Electrically and mechanically robust connections
Ensuring a robust connection between conductors is essential for a good earthing system. Mechanically coupled or exothermic welded (AXIWELD) connections can be used to create a reliable, low-impedance, and corrosion-resistant connection between conductors.
Acceptable Ground Resistance Values
The lower the grounding resistance value in the earthing system, the more important it is to ensure the effective dissipation of lightning surge energy and the safety of personnel and equipment. A lower grounding resistance value minimizes the voltage drop across the grounding system during a fault or lightning strike event, thereby reducing the risk of electrical hazards such as step and contact potentials. It also helps protect electrical systems and equipment from damage and ensures that fault currents and lightning surges are directed to the ground quickly and safely.
There is no universally accepted value for grounding resistance, as it will vary depending on the specific application, type of structure, and local codes. However, some general guidelines can help determine an acceptable grounding resistance value for most situations:
- National and International Standards: The first step is to consult the relevant national and international standards, such as IEEE, IEC, or other local regulatory bodies, which guide acceptable grounding resistance values for different applications. For example, IEEE Standard 142 recommends a maximum grounding resistance value of 5 ohms for commercial and industrial facilities.
- Type of Structure: Acceptable grounding resistance values also depend on the type of structure being protected. For example, a residential building may require a grounding resistance value of less than 25 ohms, while a large industrial facility, substation, or power plant may have more stringent requirements because of the higher risk associated with these structures.
- Safety requirements: The primary purpose of a earthing system is to protect personnel and equipment from the hazards of lightning strikes. Therefore, grounding resistance values should be low enough to minimize step and contact potentials and to ensure that any fault currents or lightning surges are safely dissipated to the ground.
In many cases, grounding resistance values of 5 ohms or less are considered acceptable for earthing systems in commercial and industrial environments. For residential applications, a value of less than 25 ohms may be considered appropriate.
Commercial and industrial environments require lower grounding resistance values than residential environments due to several factors. First, commercial and industrial facilities typically have more extensive and complex electrical systems, which increases the likelihood of damage during a fault or lightning event. Lower grounding resistance values ensure that fault currents and lightning surges are effectively dissipated, thereby minimizing the risk of equipment damage and downtime.
Secondly, the nature of equipment and processes in commercial and industrial environments tends to present a higher level of electrical hazard. Sensitive electronic equipment, high-pressure machinery, and hazardous materials may be present, requiring more robust earthing systems for safety.
Finally, commercial and industrial environments typically have more on-site workers. Lower grounding resistance values help create a safer work environment by reducing the risk of step and contact potentials, which in extreme cases can lead to serious injury or even death. By complying with stricter grounding resistance requirements, commercial and industrial facilities can ensure a higher level of safety and protection for their equipment and personnel.
It is critical to consult with a qualified professional who can evaluate your specific needs and design a customized grounding solution!
Soil Resistivity Measurements
Soil resistivity has a significant impact on the performance of a earthing system because it directly affects grounding resistance and impedance. Understanding local soil conditions is critical when designing and implementing a grounding system.
The Wenner and Schlumberger methods are commonly used to measure soil resistivity. These tests involve placing electrodes in the ground at specific intervals and measuring the resistance between them. The results can be used to determine the resistivity of the soil and inform the design of the earthing system.
Grounding methods and their applications
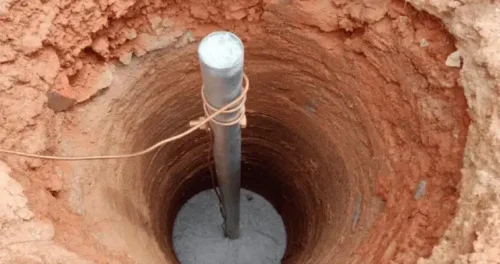
Vertical Grounding Rods
Vertical grounding rods are a common grounding method, especially in areas where space is limited. These rods are inserted vertically into the ground and connected to the structure or equipment they protect. Multiple rods can be installed in parallel to achieve lower grounding resistance.
Radial Earthing Systems
Radial earthing systems involve burying conductors radially from a center point to form a star pattern. This method provides a large area of contact with the soil, which reduces grounding resistance and improves lightning surge dissipation. Radial grounding systems are typically used in large structures and facilities such as substations and power plants.
Grounding plates
Grounding plates are flat metal conductors buried in the soil, usually shallowly. They are suitable for use in areas with high soil resistivity because the larger surface area in contact with the soil helps to reduce grounding resistance. Grounding plates can be made of materials such as copper or galvanized steel and are often used in combination with other grounding methods to improve performance.
Reverse Grounding
Reverse grounding involves the installation of a horizontal conductor around the perimeter of a building, usually at a shallower depth in the ground. This method is often used in conjunction with vertical ground rods or other grounding techniques to create an equipotential zone that minimizes step and contact potentials.
Earthing System Maintenance and Inspection
Regular inspection of the grounding system is essential to ensure its long-term effectiveness. A visual inspection should be performed to check for signs of corrosion, physical damage, or loose connections. Regular measurements of grounding resistance will also help identify potential problems with the system.
Maintenance may involve cleaning and tightening connections, replacing corroded or damaged components, and ensuring that conductive elements remain in good condition. Proactive maintenance can help extend the life of your grounding system and keep it effective over time. You can read our in-depth article for more information.
Compliance with Codes and Standards
Relevant codes and standards, such as those of the IEEE, IEC, and other local regulatory agencies, should always be considered when designing and implementing a good grounding system. Adherence to these codes ensures that the grounding system meets the necessary safety and performance requirements and is suitable for its intended use.
Design Considerations for Effective Grounding Solutions
In addition to the previously mentioned features and methods, it is critical to consider the unique needs and requirements of each specific application when designing a good grounding system. Factors such as the type of structure, location, surroundings, and potential lightning exposure should all be taken into account. By evaluating these factors, you can customize the grounding system design to provide the most effective and reliable protection.
Case Study 1: Industrial Facility
Industrial facilities located in areas with high lightning activity often experience equipment damage and power outages due to lightning strikes. The existing grounding system was outdated, had insufficient grounding resistance and impedance, and lacked proper equipotential connections. This resulted in lightning surge energy that could not be effectively dissipated, leading to ongoing problems at the facility.
To address this issue, we designed and implemented a new grounding system that took into account the unique requirements of the facility and the local soil resistivity. A thorough soil resistivity analysis was performed to help design a grounding solution that was appropriate for the specific soil conditions in the area.
By utilizing a combination of vertical ground rods, radial conductors, and grounding plates, the facility significantly reduced grounding resistance and impedance. Equipotential connections were also employed to minimize hazardous potential differences between various input conductors such as electrical systems, telecommunication systems, and metallic water services. As a result, the facility experienced reduced downtime, lower equipment maintenance costs, and increased personnel safety.
Case Study 2: Residential Complex
Residential complexes located in coastal areas are vulnerable to lightning strikes due to their proximity to the ocean. The existing grounding system did not provide adequate protection and posed a risk to residents and their electronic equipment. To improve the effectiveness of the system, a thorough soil resistivity analysis was conducted, followed by the design and installation of a customized grounding solution.
By using balanced grounding around the perimeter of the complex and using vertical ground rods at strategic locations, an equipotential zone was created that minimized step and contact potentials. In addition, surge protection devices were installed on the main electrical distribution panels to protect sensitive electronic equipment from voltage surges. The improved grounding system provides better protection for residents and their valuable assets.
FAQ
Q1: What is the purpose of an earthing system?
A1: The purpose of an earthing system is to provide a safe path for electrical faults to dissipate into the ground, preventing the risk of electric shock, equipment damage, and fire hazards.
Q2: How does an earthing system work?
A2: An earthing system works by establishing a low-resistance pathway for fault currents to flow into the ground, stabilizing voltage levels and protecting against electrical faults.
Q3: What are grounding electrodes?
A3: Grounding electrodes, such as ground rods or plates, are components of the earthing system that provide the connection between the electrical system and the earth.
Q4: Why is bonding important in an earthing system?
A4: Bonding ensures that all metallic components of an electrical system are at the same electrical potential, preventing potential differences and reducing the risk of electrical hazards.
Q5: What is the role of surge protection in an earthing system?
A5: Surge protection devices divert excess voltage caused by lightning strikes or electrical disturbances to the ground, protecting sensitive equipment and preventing damage.
Conclusion
A good grounding system is essential to protect buildings, equipment, and people from the damaging effects of lightning strikes. By understanding the key characteristics of the system, considering soil resistivity, using appropriate grounding methods, and complying with relevant codes and standards, you can design and implement an effective grounding solution. Regular maintenance and inspections will ensure the long-term effectiveness of the system, providing reliable lightning protection.
I hope you now have a clear understanding of earthing systems. At WZJ, we manufacture and supply a wide range of grounding materials, including grounding rods, grounding plates, grounding strips, grounding clamps, grounding pits, and other accessories. We also help design complete systems for your structure for substation grounding, solar grounding, and residential or commercial structures.
Website: https://www.wzjelec.com/
Product: https://wzjelec.com/product
Email: rose@sunjelec.comAuther: Leb