Ultimate Guide to Insulation Piercing Connectors: Features, Benefits, and Applications
Insulation piercing connectors are electrical connectors that utilize a joining process to pierce or replace the insulation of a wire or cable to form a conductive path to the internal conductors. They are also commonly referred to as Insulation Piercing Clips, Insulation Replacement Connectors, and Wire Tap Connectors. The use of insulation piercing connectors eliminates the need to strip the insulation from the conductors before making the connection. Below we will describe the common types and provide the advantages and disadvantages of using such insulation piercing connectors.
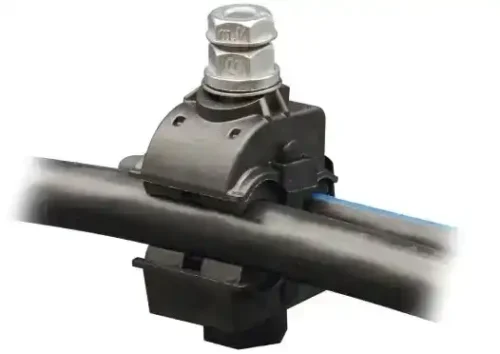
What are Insulation Piercing Connectors?
Insulation piercing connectors are specifically designed to quickly diagnose, test, or connect wires in circuits with a minimum of hassle, and are used in areas where terminal connections are difficult to reach or where disconnections are not appropriate. Available in a variety of sizes, contact types, and connection forms, their use during electrical testing is fast, efficient, and reliable as it does not involve any stripping or twisting of wires. Quick installation and minimal cleanup, as well as reliable performance, have made Insulated Puncture Connectors popular in many industries. Examples of electrical test applications include vehicle wiring harnesses, electronic locks, alarms, and network and telecom cables. These low-voltage circuits are ideal for insulation piercing connectors.
Key Features of IPCs
Durable Construction
IPCs are made from high-quality materials such as aluminum or copper, which provide excellent conductivity and durability. These materials are often coated with anti-corrosive finishes to enhance their lifespan, even in harsh environments.
Versatile Design
The design of IPCs allows them to be used with a wide range of cable types and sizes. This versatility makes them suitable for various applications, from residential wiring to industrial installations.
High Conductivity
One of the standout features of IPCs is their high conductivity. The materials used in their construction ensure minimal resistance, allowing for efficient power transmission and reducing energy losses.
Benefits of Using IPCs
Time and Cost Efficiency
One of the primary benefits of IPCs is the time and cost savings they offer. Since they do not require stripping the insulation or using specialized tools, IPCs can be installed quickly and easily, reducing labor costs and installation time.
Enhanced Safety
IPCs maintain the insulation integrity of the cables, which enhances safety by preventing accidental shorts and electrical faults. This feature is particularly important in preventing power outages and ensuring the reliability of electrical systems.
Reliable Performance
Thanks to their durable construction and high conductivity, IPCs provide reliable performance even in demanding conditions. They can handle high current loads and voltages, making them suitable for various applications.
Common Applications of IPCs
Residential Electrical Systems
In residential settings, IPCs are used for connecting wires in lighting fixtures, power outlets, and other household electrical installations. Their ease of use makes them a popular choice for DIY enthusiasts and professional electricians alike.
Commercial and Industrial Uses
In commercial and industrial environments, IPCs are used to connect large cables in distribution networks, machinery, and equipment. Their robust design and reliability make them ideal for these demanding applications.
Renewable Energy Installations
IPCs are also widely used in renewable energy installations, such as solar panels and wind turbines. Their ability to handle high currents and voltages makes them suitable for connecting the components of these systems efficiently and securely.
Performance and Reliability of Insulation Piercing Connectors
Connectors utilizing Insulation Piercing technology are designed to create a semi-permanent metal-to-metal connection between the wire and the Insulation Piercing connector. Several factors can affect its performance and the reliability of the connection. These factors include:
- The type of contact
- Connection method
- Connector tip design
The type of contact
Connection reliability has a direct impact on the performance of a connector where the insulation is pierced during electrical testing. The most commonly used contacts consist of a single pin or a group of multiple pins, often referred to as a “bed of nails”. The number or size of these pins piercing the insulation directly affects the quality of the connection.
The right type of contact for your application is critical. Too small and the needles will have difficulty breaking through the insulation, making the connection weak or intermittent and producing misleading results. Too large and the hole created by the needle will not repair itself and will likely damage the conductor due to corrosion or dirt bypassing the insulation. The bed of nails contact type is often preferred for smaller gauge cables because a single pin can easily miss the internal conductor. Bed of nails increases the reliability of establishing a positive connection
Connection Method
Another important factor affecting the reliability of Insulation piercing clips is the method of connection. Sufficient force to hold the contact interface in place is essential to ensure a strong and reliable connection for electrical testing. Connection methods are generally suitable for different applications and available methods include screw-in, spring-loaded, and hand force. Some methods will combine both to maximize the likelihood of a good first-time connection. Below we will look at the different methods and explain their advantages and disadvantages.
Screw-in connections
Screw-in insulation piercing clips are slower to install than both spring-loaded and hand-piercing connectors. This is even though this type of connection is stronger and more reliable over a longer period of electrical testing. However, reasonable access to the wires is required to ensure that the technician can tighten the piercing connector for a good connection.
Advantages:
- Hands-free testing
- Personal assurance that connectors are tight
- Very reliable connection
- Strong
Disadvantages:
- Slow to install
- Excessive pressure may damage the internal wire harness
- Limited to applications where wires are accessible enough and screwable connections can be made.
Spring Connection
Insulated Puncture Connectors with spring connections rely on the tension of a spring to insert a pin into the insulation to make contact. A spring is an elastic object that stores mechanical energy. The energy of the spring depends on the size, material, and number of coils. The handheld nature of these probes typically limits the maximum voltage capacity.
Advantages:
- Reliable connection
- Fast connection
- Cost-effective
Disadvantages:
- Shorter service life because the spring eventually wears out, resulting in a weaker connection
- Weak springs can make it difficult to pierce the hardened insulation that is often found on old wires, which harden with heat
Connector tip design
The tip of an insulation piercing connector has a shape designed to help locate the connected wires. This usually takes the form of a “V” or “U” shape, with a radius that fits so that the wire the connector is designed for is centered underneath the tip. It is also possible to find tips with extended hooks, which are embedded in the needle to capture the wire in the jaws.
It is important to select an Insulation piercing connector that fits the range of wire diameters you want to use. Ideally, the wire is centered on the tip so that the needle can pierce the wire right in the middle. If the tip is too large for a small diameter wire, the wire may not be positioned correctly in the tip and the needle may miss the conductor or make a poor connection. If the connector tip is too small for a large diameter wire, the pin may push the insulation aside and miss the conductor again. This is especially important if it is difficult to see the connection point when making the connection.
The “V” shaped tip has the greatest adaptability to a wider range of wires and the technician can assist in the connection process by gently pulling the connector over the wire to help center it at the bottom of the “V”.
Conclusion: Insulation Puncture Connectors
Insulation piercing connectors are useful in many applications, the most common being automotive diagnostics, telecommunications, security alarms, and decoders. Many specialized connectors on the market use different contact types, sizes connection types, and different tip designs to help locate wires. To select the right Insulated Puncture Connector for your application, it is recommended to use a “work backward” approach and evaluate the wires you plan to test. Then, determine your exact Insulation Puncture Connector requirements based on wire diameter capability, contact type, and connection method. There are many electrical strain relief connectors for different applications, but using the right tools often makes the task faster, safer, and more accurate.
Conclusion
Insulation Piercing Connectors are a vital component in modern electrical systems, offering a range of features and benefits that enhance the efficiency, safety, and reliability of electrical connections. Their versatile design, ease of installation, and durable construction make them suitable for a wide range of applications, from residential wiring to industrial installations. By understanding the key features, benefits, and applications of IPCs, you can make informed decisions and ensure the success of your electrical projects.
FAQs About IPCs
What is an Insulation Piercing Connector?
An Insulation Piercing Connector (IPC) is a device that allows for the connection of electrical cables without stripping the insulation, using sharp teeth to pierce through and make contact with the conductor.
Are IPCs safe to use?
Yes, IPCs are designed to enhance safety by maintaining the insulation integrity of cables, and preventing accidental shorts and electrical faults.
Can IPCs be used in outdoor installations?
Absolutely. IPCs are designed to be weather-resistant and can withstand various environmental conditions, making them suitable for outdoor installations.
What types of cables are compatible with IPCs?
IPCs are compatible with a wide range of cable types, including copper and aluminum cables, making them versatile for different applications.
How do I choose the right IPC for my project?
Consider factors such as the type of cables, environmental conditions, and specific project requirements. Look for connectors that meet industry standards and are certified for your application.
Website: https://www.wzjelec.com/
Insulation Piercing Connectors: Piercing Connector – wzjelec.com
Email: rose@sunjelec.comAuther: Leb

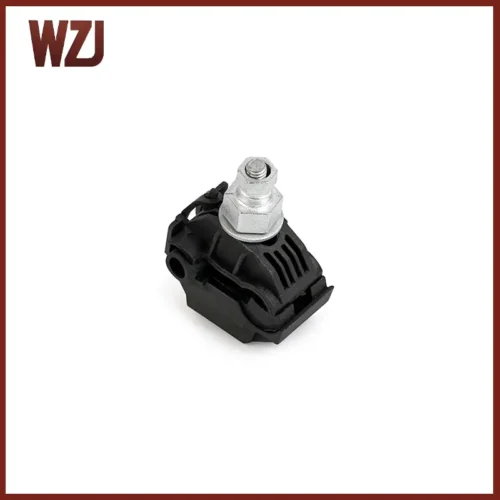

WHY CHOOSE WZJ INSULATION PIERCING CONNECTORS
WZJ was established in 2004 and has been manufacturing Insulation Piercing Connectors since 2015 and has experience in many international projects.
Here are some of the factors that make WZJ one of the best manufacturers and why you should buy IPCs from WZJ.
- Product Quality and Reliability: WZJ produces high-quality Insulation Piercing Connectors that are reliable and durable.
- Compliance and Certification: WZJ Energy ensures that the Insulation Piercing Connectors comply with relevant industry standards such as NFC 33-020, and EN-50483, giving customers confidence in the quality and safety of their products.
- Product Range: WZJ Energy offers a wide range of Insulated Puncture Connectors for 1kv power lines to meet various application requirements.
- Research and Development: WZJ Energy invests in research and development to continually improve the design, performance, and reliability of its Insulated Puncture Connectors to ensure they remain competitive in the marketplace.
- Customer Support: WZJ Energy offers strong customer support including technical assistance, flexible OEM with sticker, and after-sales service, which is important to customers looking for reliable application solutions.