Electrical Lug Buying Guide: 5 Essential Tests You Must Know
Trust but verify. This concept applies not only to everyday life but also to electrical components such as electrical lugs. There are countless electrical lug manufacturers around the world, and many overlook the importance of regular product testing. This raises a simple but vital question:
Do you trust your cable lugs?
WZJ has been manufacturing a wide range of electrical lugs and connectors for over 30 years. Our products include copper, aluminum, and bimetallic lugs used in a variety of applications such as solar power plants, substations, transformers, control panels, switchgear, and more.
In this blog, you will learn how to ensure the quality of your cable lugs by understanding the necessary electrical and mechanical tests. After reading this article, you will familiarize yourself with the following tests:
- Conductivity testing
- Thermal cycling test
- Tensile testing
- Safety test
- Pull-out test
But first, let’s briefly discuss lugs and their importance to electrical safety.


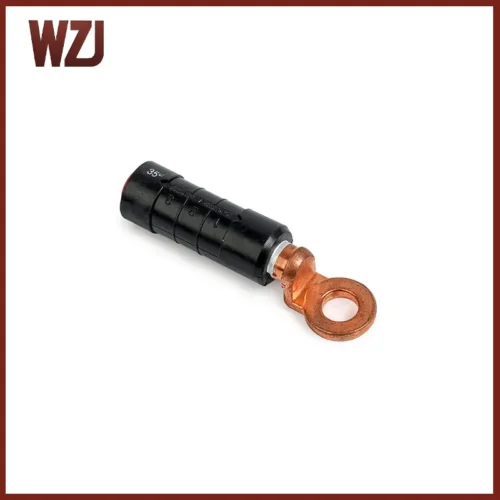
What are electrical lugs?
Electrical lugs are components used to connect a wire or cable to another electrical component or termination point. They are designed to create a strong, mechanically strong, and electrically conductive connection between a conductor and the component it is connected to.
If it is not possible to connect the conductor directly to the device (due to space constraints, different conductor sizes, etc.), a lug is required. Electrical lugs are mainly made of copper, aluminum, or bimetallic (a combination of copper and aluminum).
Lug Types
The market offers various types of lugs, each with a specific application. Some popular types include:
- Copper lugs: ideal for high conductivity connections.
- Aluminum lugs: lightweight and cost-effective, best suited for aluminum conductors.
- Bimetallic lugs: used to connect copper cables to aluminum terminals.
- Pre-insulated Lugs
Choosing the right electrical lug
Factors to Consider
When selecting electrical lugs, consider factors such as material, size, insulation, and the specific requirements of the application.
The Importance of Certification
Look for lugs that are certified by a recognized standards organization to ensure they meet industry requirements and pass rigorous testing.
Recommendations
Choose a reputable brand and consult a professional to select the best lug for your needs. WZJ’s professional engineers are ready to answer your questions!
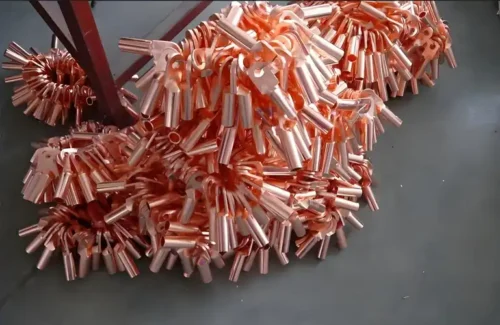
Testing electrical lugs: 5 test types
1. Conductivity Test
Purpose: Measure the conductivity of the lugs to ensure the quality of the lugs.
This test is performed using a conductivity tester that measures the conductivity of a metal in percent according to the International Annealed Copper Standard (IACS). Pure copper is considered 100% conductive.
For copper lugs, the conductivity must exceed 97% to be Electrolytically Tough (ETP) grade copper. At WZJ, our copper lugs have a conductivity of 99% IACS, ensuring a high-quality copper material.
2. Thermal Cycling Test
Purpose: To evaluate the long-term performance of lugs under different thermal conditions.
The purpose of this test is to evaluate the long-term performance of the lugs. How do we perform this test? We form a test loop by connecting several lugs in series with suitable cables. We then evaluate the functional characteristics of six lugs and a reference conductor. The reference conductor is part of the loop and we control its temperature to about 120 to 140 degrees Celsius by injecting current.
After all the lugs and the reference conductor are heated and stabilized, they are cooled back to ambient temperature. We repeat this heating and cooling cycle 1,000 times, which takes about 2 months to complete. If the lugs meet the resistance and temperature standards of IEC 61238, our lugs have been tested and proven to have a long service life.
Note: There are two different types of tests for lugs. The test described here follows the IEC 61238 guidelines, while the other test follows the UL 486-A 486-B current cycling test. However, both tests are performed in our lab using the same equipment.
3. Tensile Testing
Purpose: To determine if the lugs can withstand the required tensile load.
The purpose of this test is to determine if the lugs can withstand the required tensile load without being damaged. How do we perform this test? The test is performed on a tensile testing machine. We set the required tensile load value and the duration of the applied tensile load for 1 minute according to Table 4 of IEC 61238.
If the slip does not exceed 3 mm, the sample complies with the standard. As you can see here, there is no damage to the lugs and no slippage of the conductors. This confirms that it can handle the tensile loads required in practical applications.
4. Safety Test
Purpose: To ensure that the cable lugs remain securely attached to the cable despite mechanical stresses.
This test ensures that the cable lugs remain firmly attached to the cable under mechanical stress and prevents any accidental disconnection.
How do we perform this test? The lugs are first crimped onto the cable using the specified crimping tool and the specified number of crimps. We have a separate video on how to crimp cable lugs, the link to which is here and in the instructions.
Finally, install the crimped lugs along with the cable in the safety test equipment. Attach the weights specified in the UL486A/486B standard to the cables. These cables are rotated for the time specified in the standard. The cables should not slip off the lugs after the specified time has been completed. For lugs manufactured by WZJ, no slippage was observed. This confirms that WZJ lugs are securely attached to the cable even under mechanical stress.
5. Pull-Out Test
Purpose: To verify the mechanical strength of the bond between the lug and the cable.
This test determines the mechanical strength of the bond between the cable gland and the cable.
How do we perform this test? The test is performed by UL 486A 486B. The lug is first fixed to a standard cable and then subjected to a gradually increasing direct tensile load.
The force applied during this test is measured in kilonewtons. The standard requirement is that the lugs must be subjected to a minimum pull-out force, depending on their size and design. For example, this WZJ copper lug is expected to withstand a pulling force of over 1,000 Newtons (i.e., 1 kiloNewton).
This test verifies that the connection between the lug and the cable will remain strong and intact even under extreme pulling forces. This is important because electrical connections should not be compromised by mechanical stress.
How the Pull-Out Test is Conducted
- Secure the lug to a testing apparatus.
- Apply a steadily increasing force to the cable.
- Measure the force at which the cable detaches from the lug.
Frequently Asked Questions (FAQ)
What are electrical lugs used for?
Electrical lugs are used to securely connect cables to appliances, surfaces, or other cables.
How do I choose the right size electrical lug?
The size of the lug is selected based on the size of the cable and the specific requirements of the application.
Why is it important to test electrical lugs?
Testing ensures that lugs meet industry standards for safety and performance, preventing potential failures and hazards.
Can I perform these tests at home?
While some tests can be performed at home with the proper equipment, it is recommended to rely on professional testing to ensure accuracy and compliance.
What certifications should I look for?
Look for certifications from recognized standards organizations such as UL, IEC, or CSA to ensure that lugs meet industry requirements.
Conclusion
Understanding and performing these tests is essential to ensure the quality and safety of electrical lugs. All WZJ-manufactured lugs are subjected to these tests to IEC 61238 and UL 486A/486B standards at Axiom Laboratories in Mumbai. The laboratory is accredited by the National Accreditation Board for Testing and Calibration Laboratories (NABL) and approved by Underwriters Laboratories (UL).
WZJ has over 30 years of experience in manufacturing and supplying a wide range of electrical lugs to over 100 countries. Our team of over 50 engineers can help you design and install lugs, connectors, and lightning protection systems.
Our products are trusted in solar farms, data centers, and even everyday residential buildings. If you’d like to learn more about insulators, lightning protection, grounding systems, or other electrical engineering topics, subscribe to our weekly newsletter or check out our other blog posts.
Stay safe and make sure your lugs are properly tested and compliant!
Thank you for reading the blog, WZJ is a leading manufacturer and supplier of electrical components sold in over 80 countries. Please visit our Contact Us section to speak to one of our industry experts.
Website: https://www.wzjelec.com/
Email: rose@sunjelec.comAuther: Leb