The Ultimate Guide to Cable Terminals: All Types and Functions
Electrical and electronic equipment requires cables for power supply, distribution, interconnections, control, monitoring, and so on. Some of the devices that come to mind include appliances, electrical load switches, circuit breakers, fuse holders, motors, generators, transformers, busbars, and electrical control and distribution boards. In addition, many mechanical devices require cables to connect electrical systems including control, monitoring, and power supply. Wherever electricity is used, cable terminals are a necessity. It is therefore vital that these cable connections are robust, strong, and safe, and cable terminals ensure that this is the case.
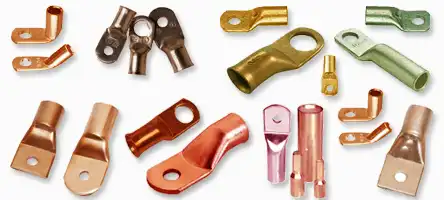
What are cable terminals?
A cable terminal, also known as a cable lug, is often defined as a fixture that is installed at the end of a cable (or wire or conductor) to ensure that the cable is properly connected to the device, system, or equipment.
Cable terminals connect cables to various devices, in addition to helping current flow through them. As such, they create strong connections that hold electrical systems together.
Without the use of cable terminals, cable connections in an electrical system would be very difficult to trust unless some permanent method, such as soldering, is used. Improper and poor-quality cable connections can lead to high resistance at the joints, which can lead to overheating, flashover or short circuits, and fire hazards. These terminals are critical factors in the design, construction, maintenance, repair, and replacement of electrical system components. In addition, if properly selected and used, they ensure long-term reliability.
Cable terminals are primarily used for cable connections in electrical systems, equipment, and installations. They are designed to accommodate a wide range of cable sizes, including large cross-section cables. They are robustly designed to support the weight of the cable and carry the high currents for which they are designed.
The most commonly used cable terminals are made of copper or aluminum or their respective alloys (i.e., copper alloys or aluminum alloys).
Here, we take a closer look at cable terminals – their types, uses, and international standards.
Copper cable terminals
Copper cable terminals inherently have the high conductivity of copper and are easy to install and durable. These terminals are made of high-quality ETP copper material and tinned for added corrosion resistance. They are particularly beneficial for outdoor applications or use in marine environments.
Aluminum Cable Terminals
Aluminum cable terminals are made of high-grade aluminum and are lighter and less expensive than copper cable terminals. Aluminum cable terminals and cables are very economical and therefore widely used.
Tinned Copper Cable Terminals
Tinned copper terminals, commonly known as tinned copper terminals, are resistant to corrosion caused by harsh environments. Tinned copper is mainly used to prevent oxidation and corrosion. Tin serves as an additional layer of protection against corrosion, oxidation, and high-temperature damage. These terminals are ideally suited for large-scale applications in electrical systems and grounding systems. The main disadvantage of tin as a metal finishing process is that it is not suitable for use at high temperatures (about 200 degrees Celsius).
Bimetallic cable terminals
When two dissimilar metals come into contact with each other, they can cause “dissimilar metal” corrosion or “electrochemistry”, i.e. the formation of an electrically conductive path that moves electrons and ions from one metal to the other. This results in the corrosion of one metal as its ions are deposited on the other metal. This may occur, for example, in the following situations:
- Aluminum cables are terminated on copper busbars
- Aluminum cables are “capped” with copper terminals
Aluminum cables and copper lug tubes are two different metals and can therefore react electrochemically. Therefore, bimetallic terminals are used to prevent this differential contact. These terminals are made by connecting forged copper palms to aluminum tubes using a solid-state welding process called friction welding. As a result, these terminals are protected from galvanic corrosion and the joints are robust.
In a bimetallic terminal, the aluminum barrel will hold the aluminum cable and make contact with it, while the flat copper palm will make contact with the copper busbar. The copper palm is provided with holes so that it can be bolted to the copper busbar. Bimetallic terminals are widely used for wiring switchgear panels, and distribution boxes (often called sink boxes) in solar power plants and other electrical systems. Some of the common types of cable terminals we see are:
- Ring terminals
- Pin terminals
- Fork or “U” type terminals
- Flat terminals
Ring terminals
Ring terminals are terminals that connect cables or wires to a stud or screw connection. One end of the ring terminal is equipped with a closed or open crimp barrel to establish an electrical connection to the cable. These cable terminals are made of high-grade copper with high conductivity and purity. Ring terminals are reliable and are used in situations where the possibility of the terminals being removed from the terminal block is less due to their ring shape.
These terminals are available in different types such as insulated, uninsulated, and metal reinforced. Ring terminals are widely used for terminating wires in houses, buildings, switchgear, and other electrical equipment. These terminals are reliable and safe due to their shape and the possibility of slipping out of the terminal block is very low.
Pin Terminals
Pin terminals are used in industrial and commercial applications. They are tubular and made of lightweight aluminum with brass lug nuts for durability. Pin terminals are robust and reliable. They are designed for terminating cables into junction boxes. Reduced pins make these terminals ideal for terminating conductors into contact block applications.
These terminals are primarily used in industry to connect cables to relays and other electrical instruments. The “I” shape makes them easy to connect. It is used for low voltage levels as well as for control and indication cables.
Fork (or “U”) terminals
Fork terminals are similar to ring terminals, except that they are “U” shaped and designed for quick and easy connection and disconnection.
In some cases, it is difficult to remove the nut from the stud when disconnecting a wire, or the workspace is very small. In these cases, fork terminals are an excellent choice. While ring terminals need to be slid over the stud, fork terminals only need to be tightened against the stud. Therefore, fork terminals can be installed without completely removing the nut from the stud. Simply partially loosen the nut, slide the fork terminal behind the nut, and retighten. This is especially beneficial when multiple wires are already attached to the busbar stud; no wires or equipment need to be removed to make room for other terminals.
Fork terminals are commonly used for connections to devices such as miniature circuit breakers, switches, relays, and other electrical instruments.
Flat Terminals
Flat terminals are similar to pin type and are also “I” shaped. As the name suggests, they are flat in shape, whereas pin terminals are tubular. Flat types are also commonly used for low-voltage control wiring.
International Standard for Cable Terminals
Cable terminals are a very critical part of the electrical connection, and as such, they must be certified by a reputable international body. Certification is based on the design, materials, construction, and testing of cable terminals. These are defined by standards set by the IEC (International Electrotechnical Commission), UL (Underwriters Laboratories), and DIN (German Association for Standardization).
The following international standards apply to cable terminals.
IEC 61238-1
This standard applies to the electrical and mechanical properties of power cable connectors.
The electrical and mechanical tests to be performed are defined in this IEC standards document.
UL 310 and UL 486A 486B
This standard evaluates the safety of cable connectors and compliance with standards.
It defines the electrical and mechanical tests to be performed for this purpose.
DIN 46235, 57295
This standard defines the application, dimensions, and marking of cable terminals.
The standard also guides the selection of suitable cable terminals for various types of conductors and cables.
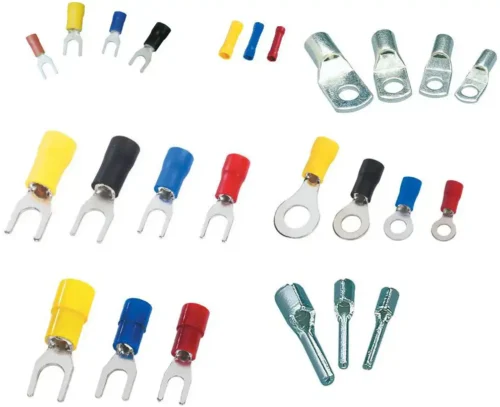
How to Choose the Right Cable Terminal
1. Determine the Application
Consider the environment and application where the terminal will be used. For example, automotive applications may require terminals that can withstand vibrations and temperature fluctuations.
2. Check the Wire Size
Ensure the terminal is compatible with the wire gauge you are using. Using the wrong size can lead to poor connections and potential failures.
3. Consider the Material
Choose terminals made from materials that suit the environment. For instance, brass terminals offer good conductivity and corrosion resistance, while nylon-insulated terminals provide additional protection against moisture and chemicals.
4. Inspect the Insulation
Insulated terminals offer added protection against electrical shorts and are often used in applications where safety is a concern.
5. Ease of Connection
Consider how often the connection will need to be made and broken. Quick disconnect terminals are ideal for applications requiring frequent disconnections.
FAQs
- What are cable terminals used for?
Cable terminals are used to connect electrical wires to devices or other wires securely, ensuring reliable electrical connections.
- How do I choose the right terminal for my project?
Consider the application, wire size, material, insulation, and ease of connection to select the appropriate terminal.
- What tools are needed to install cable terminals?
A proper crimping tool and wire stripper are essential for installing cable terminals securely.
- Can I use pliers to crimp terminals?
No, using pliers can damage the terminal and result in poor connections. Always use a proper crimping tool.
- Are insulated terminals necessary?
Insulated terminals provide added protection against electrical shorts and are recommended for applications where safety is a concern.
Conclusion
Cable terminals have a wide range of applications in cables and terminals depending on their type and material composition (i.e. copper, aluminum, copper-aluminum alloys).
The various types of cable terminals and their uses have been mentioned above. They are used for wiring and cabling in houses, buildings, electrical equipment, switchboards, switchgear, electrical consoles, industries, substations, road lighting, appliances, electrical systems, solar power plants, and the list goes on and on. Cable terminals are complementary to cables.
Copper cable terminals have the high conductivity of copper itself, are easy to install, and are durable. Aluminum cable terminals and aluminum cables are very economical and therefore widely used. Tinned copper terminals (often called tinned copper terminals) are resistant to corrosion caused by harsh environments. Bimetallic terminals are widely used in switchgear panels, solar power plant distribution boxes (often referred to as converter boxes), and other electrical system wiring.
Although these terminals represent a very small portion of electrical systems and equipment in terms of size and cost, they are extremely critical. They are critical in the design, construction, maintenance, repair, or replacement of electrical system components. Cable terminals are an important part of an electrical system used for current passage. Proper selection of cable terminals is very important and depends on the following factors:
- Cable size, material, and type
- The load current
- How much weight the cable terminal needs to carry
- Surrounding or environmental conditions (e.g. temperature, corrosive environment, etc.)
Improper selection or installation of cable terminals can lead to overheating of the terminals, which can lead to electrical short circuits and fire hazards. Properly selected and installed cable terminals can withstand harsh environmental conditions, thus ensuring long-term reliability. Unfortunately, in many cases, cable terminations are not taken seriously. Oversized terminals are used to cause cable terminals to come loose, while undersized cables are either forced into the terminals or cable strands are cut to make them fit into the terminals. Both of these methods are most likely to result in a fire hazard due to overheating or short-circuiting at these cable terminals.
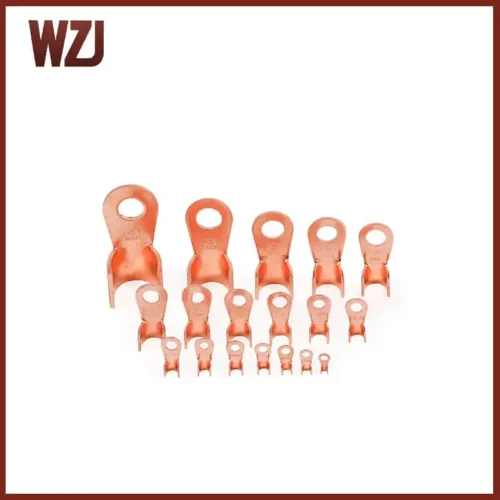
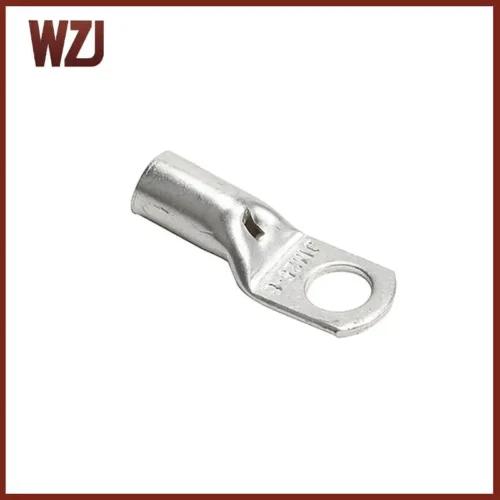
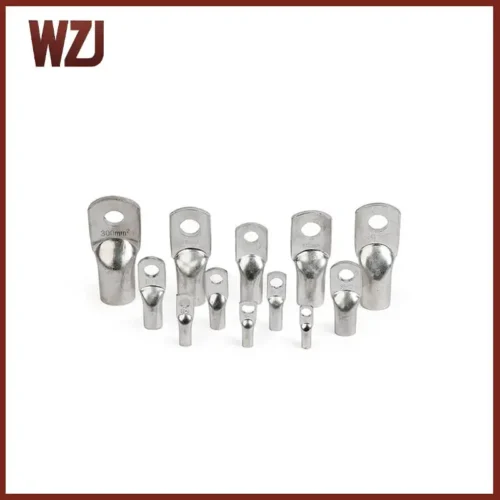
For more information, please feel free to contact us
Website: https://www.wzjelec.com/
Auther: Leb
Product: https://wzjelec.com/product
Email: rose@sunjelec.com